In 1972, ishida, a Japanese company, introduced what seemed an unusual weighing machine at the time, a cone machine composed of eight pressure scales. The main purpose of this machine was to automatically pack and weigh green peppers, with an accuracy range of 150± 2G and a speed of 50-60 bags/min. This was the Multihead Weigher, as we now know, which changed the rules of the game and proved to be the best weigher in many industries. At that time, the packaging industry was in urgent need of an accurate and reliable weighing and discharging system, and the Multihead Weigher was destined to be a great product.
History
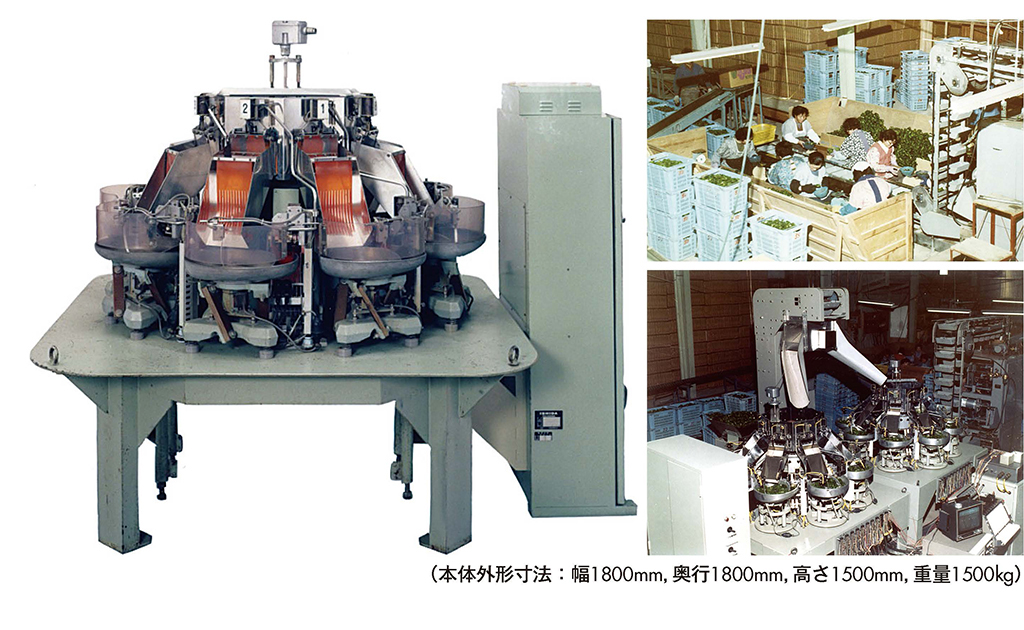
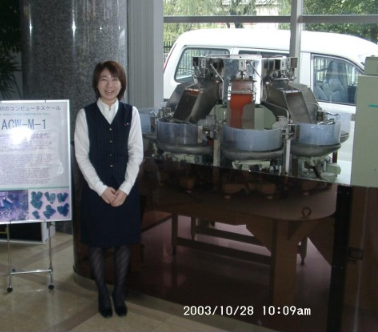
By the 1980s, the speed of Multihead weigher from Ishida had increased to 160-180/min, and they stepped into other fields, such as candy, meat, metal parts, rubber parts, etc. More importantly, not only did Multihead weigher help Ishida dominate the packaging market in Japan but also made it develop into an international enterprise. First of all, in 1978, the first Australian companies bought their products, By 1980, a U.S. company called Heat and Control Inc. signed a contract with Marketing contract, then president Ishida Ryuichl or Circle of Honor Award’s first non-American recipient. They once possessed 80% of the weighing packaging market, but with the progress of technology and development, when the Multihead weigher core technology is no longer a secret, Imitations from Asia come at a staggering price, and Japanese and American packaging-machine makers have come up with products as good as Ishida’s. The industry has grown by working closely with manufacturers and users, and now buyers of multihead weigher have a myriad of options.
Over the years, the Multihead weigher category has evolved for specific products, such as those with a smooth finish, a specially handled chute and a specific jitter frequency, and fragile items with shorter drop distances and cushioning pads. The weighing of mixed products can be achieved by group weighing, and in recent years spiral channels and Teflon coating solutions have been developed for handling sticky or wet products(Such as cheese). The multi-weight scale has so far dominated the market, becoming one of the few, perhaps the only, solid package weighing solutions available, and it’s still evolving.
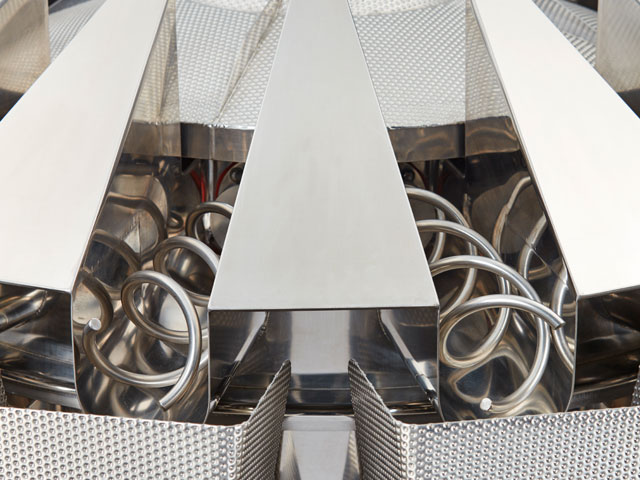
Working Principle
Although Multihead Weigher has changed the packaging industry to some extent, its principle is not complicated. Its general principle has not changed much in the past 50 years, and it is mainly divided into feeding, combined weighing, and discharging
Loading
First need to package material through various ways into the known as dispersion table in the middle of the bump on the top of the cone, this part will be in accordance with the set frequency and amplitude of vibration, made with the vibrations of the material and the vibration of the kinetic energy to overcome the friction to the gravitational potential energy of material in lower edge of the slide, slide around the dispersion around the table of radial troughs, and dispersion table similar to the radial troughs will jitter, slide it further into a device called Hoppers, into which the material falls. The vibration of the radial troughs and dispersion table independent are independent of each other, each radial trough is equipped with a hopper respectively. Dispersion under the table and simple weighing module, when they tested the dispersion table of the less material, will send signals to the material added to the dispersion of the table. This process, the dispersion table the frequency and the amplitude of vibration influence of the landing speed and eventually blanking weight, this needs to be set according to the material surface friction, experienced engineers often can quickly find the right frequency and amplitude. With the exception of the use of radial towards, some special products may use Tim or Screw Systems to drive the material, with similar principles. Dispersion of other Multihead weigher table of ladder-type, high top and bottom of the ladder short, parallel hoppers are arranged on the bottom of the ladder.
Combined weighing
The material falling from the edge will enter Hoppers, and the material will stay in poll Hoppers above hoppers, and after the appointed time the vibration is stopped, there is a weighing hopper below, and if the weighing hoppers are empty, each weighing hoppers will drop the material into the lower weighing Hoppers, and each weighing hoppers has a weighing function. The central control system for Multihead Weigher combines all the weighed hopper data to select the Combination solution closest to the weight set by the user (which is why Multihead weigher is also called Combination weigher). It is not difficult to understand that the more hoppers, the more accurate and faster the weighing, so the multi-head scales will develop from the earliest 8 to as many as 20 or even 30. Some products and additional Booster Hoppers are used to store the materials that have been weighed.
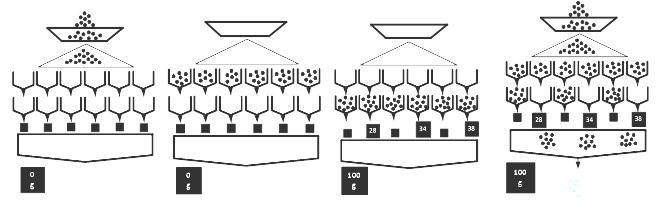
In fact, this step is the main difference between most different Multihead weighers. The contents of each weigh X (X=1,2,3… N), and x is basically accord with normal distribution, and set it as n (mu, sigma) and the weigh hoppers independent each other, each time the random k when feeding hopper, then tick k mu is packaging accuracy index, however, modern Multihead weigher is master, calculation of the optimal feeding after so usually will be more close to the target weight, when feeding weigh hoppers subset of H, sigma squared package = VAR Σ ∈ x H (x). M. Salicru and J. J. Barreiro have published many papers on weighing accuracy, Keraita JN and Kim KH have done a lot of research work related to increasing the feeding speed, and there are also many products using such as Bi-criteria optimization model and Priority. These are highly specialized fields, which make even Multihead weighers of the same principle differ greatly in speed and precision. Of course, engineers play a large role, and reasonable parameter Settings can greatly increase accuracy. Perhaps we will have a special article later on the combinatorial algorithm and strategy model of feeding selection.
Feeding
The final process was very simple. The selected Hoppers drop materials into discharge chute and send to packaging or other downstream machines. After Hopper is emptied, the radial Troughs will be performed again, the materials are transported into Hoppers, then cyclic weighing is performed.
Through these processes, the final combined weight error is 1-2 orders of magnitude smaller than the direct weighing importance. These accurately weighed materials can be sent to packaging bags and finally sold on the shelves, becoming commodities in your hands and mine.
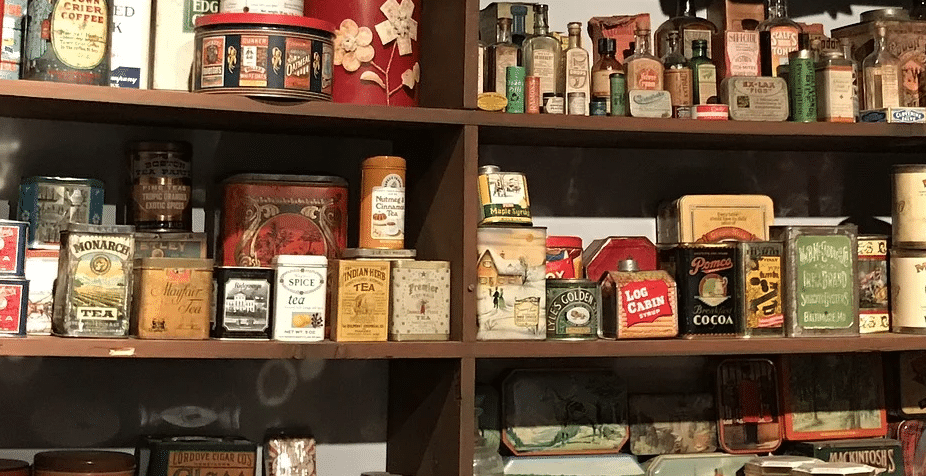
Refer:
MECHANICAL ENGINEERING HERITAGE NO.89 Multihead Weigher ACW-M-1
https://www.jsme.or.jp/kikaiisan/heritage_089_en.html
Salicrú, M., González, C. and Barreiro, J.J., Variability reduction with multiweighing proceedings
Barreiro, J.J., González, C. and Salicrú, M., Optimization of multiweighing packing proceeding
Keraita, J.N. and Kim, K.H., A study on the optimum scheme for determination of operation time of line feeders in automatic combination weighers, Journal of Mechanical Science and Technology
Ferguson Evans, The Rise of the Japanese Specialist Manufacturer: Leading Medium-Sized Enterprises